(
Shortlines, Reporting Mark: CIRY/DRSX) In this blog, searching with the keywords "Central," "Illinois," and "Railroad" produces a lot of false hits. So I'm now including the reporting marks.)
(Update: These notes describe what Shortlines calls Operation #1. For some action on Operation #2, see
Central Park Avenue Junction.)
Please follow the "Shortlines" link above for a description of this railroad. Central Illinois operated
CB&Q's 1860s industrial park between 2000 and 2010. (In fact, the last day was Aug 9, 2010. [
RobertJordan])
Ed has a
Flickr photo of their EMD switchers sitting in their yard. His comment taught me that their headquarters was at
918 W. Cermak Road. If you look at a recent satellite image, you will not see a yard. But once again we can use the birds-eye view as a time machine and see where the yard was.
As part of my trip to get pictures of the
Fisk Generating Plant before it is torn down, I took quite a few pictures of the BNSF/CB&Q track that is still left in this area.
The branch of the eastern "yard track" that sharply angled to the east with crossing signals and went along Cermak as the Lumber district is now gone.
But the part of the eastern "yard track" that crossed Cermak into an industrial area still exists. However, the crossing signals have been removed and the flangeway has filled up in stretches. Satellite images show the area between the two forks and between Canalport and Cermak to be a storage area. But when I was there in the Summer of 2015, it was vacant land.
Update:
 |
Edward Kwiatkowski posted
The Central Illinois Railroad (Shortline) at
work switching a former C,B & Q
industrial branchline, in Chicago's
Pilsen neighborhood near Cermak
Road and Canalport Street.
Chicago Illinois. Friday, October 31st 2008. (Defunct.)
In 2015 I took six photos of the line that Ed's train was on. I started shooting from Canalport and walked south across, and then along, Cermak. The fancy rubberized crossing shown in Ed's photo is gone. But the main crossing still existed including the crossing signals. Also, even the smokestack of the old Fisk Power Station exists even though its boilers have been cold for many years
That track led to a lumber yard that received centerbeams until 2007. The CIRY later stored their parts locomotive on that track. It remained there after the BNSF takeover. Once the locomotive was sold and moved off the line, the track was pulled up.
|
These are the six photos I took of the route that Ed's train is on.
 |
From Canalport Avenue looking southish |
 |
The turnout for the left fork we saw above is gone as is the crossing in Cermak Road. |
 |
The right fork continues to cross Cermak and the crossing signals still exist. Note that the smokestack of the Fisk Electric Power plant still stands even though the boilers have been cold for years. |
 |
That fork curves west to follow along the south side of Cermak. |
 |
Fisk could also receive coal from barges on the South Branch, so I don't know how many coal cars it used to receive. |
 |
I walked along the track by Cermak and then turned around to get this shot of weeds, brown rail, filled in crossings, and turnouts for industrial spurs that go nowhere. |
They were putting these Blackhawk figures up because we had just won the Stanley Cup.
By the time I was done taking pictures of the old BNSF/CB&Q tracks, they were almost done.
 |
John DeWit Woodlock II posted
CIRY 1206;1209 @ Sangamon Ave-Chicago,IL 06 AUG 10. |
Note the Central Illinois "headquarters" no longer has any rolling stock. It is just a storage area now with a fence. But Google has this labeled
Spanish with Salas, so it appears a building is going to soon be built here.
 |
John DeWit Woodlock II posted
CIRY 1209 @ Sangamon Ave-Chicago,IL 09 AUG 10. |
When I visited the area in 2015 to get photos of the track and Fisk, the triangle was just weeds and track. Below is one of
many photos I took of the track that is left along Cermak Road.
 |
20150705 2571 |
 |
John DeWit Woodlock II posted
CIRY 1209,1206 @ Battaglia Foods-Chicago,IL 09 AUG 10. |
 |
John DeWit Woodlock II commented on his posting
Go to Ashland Ave between Blue Island Ave on the north and the Chicago River on the south. The tracks were just west of Ashland behind the buildings fronting the west side of the street. Looking at Google Earth. The tracks between Blue Island and Battaglia have been removed.From north to south , there is a trapazoidal shaped parking lot, three builds in a cluster, two more parking lots, another warehouse type of building, a street that Ts off going north and south (this is how you get to the shot-by turning left/south-to get to the boat storage yard as well) along the west side of Battaglia ( the next warehouse on the south side of that short street). The yellow line in the center is Ashland Ave. Enlarge the picture to get a bit of detail. |
 |
John DeWit Woodlock II posted
CIRY 1209,1206 @ Battaglia Foods-Chicago,IL 09 AUG 10. |
 |
Street View, crossing is in 18th Street
[The satellite image still showed the track going south to 18th Place.] |
John DeWit Woodlock II posted two photos with the comment: "
DSRX (CIRY) 1208 @ Carpenter Street-Chicago,IL 02 APR 01."
I used to drive the 21 Cermak bus and would occasionally see them switching out Colonial Brick or even Kramer. I still kick myself for not doing more with this outfit.
 |
1 |
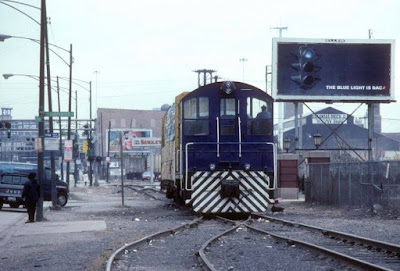 |
2 |
 |
Dennis DeBruler commented on John's posting
I'm glad you included CIRY in parens because when I Google "DSRX railroad," it keeps changing it to DSRC. And DSRX currently stands for Downeast Scenic Railroad. This is what it looked like in 2015. I'm standing on the asphalt entrance to the power plant that the Jeep is turning into in your second photo. |
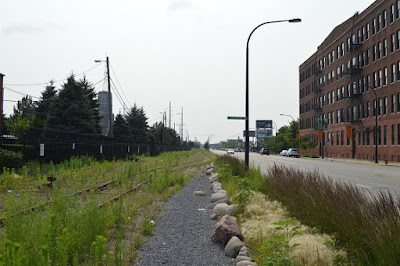 |
Dennis DeBruler commented on John's posting
The view from the same location looking West. Note the switch stand that is still standing in the weeds. |
 |
Dennis DeBruler commented on John's posting
It was not the only switch stand that still existed even though the turnout goes to nowhere. |
 |
John DeWit Woodlock II posted
CIRY 1206,1209 @ Throop Street-Chicago,IL 09 AUG 10. |
 |
Dennis DeBruler commented on John's posting
A block further west, Loomis Street. The tall, white building blends in with the light blue sky and is hard to spot. Looking with Street View, a lot of the buildings on the left in your photo are gone, which explains why I favored the old tower on the right. |
 |
John DeWit Woodlock II posted
CIRY 1206 @ Loomis Street (Kramer)-Chicago,IL 09 AUG 10.
[Looking at street views, Kramer has made has made a lot of changes on their property. For example, torn up the track and added paved parking.] |
 |
Dennis DeBruler commented on John's posting
Now I understand where this industrial spur between buildings off of Cermak used to go. |
 |
Dennis DeBruler commented on John's posting
An overview of this industrial spur crossing Cermak. |
 |
Dennis DeBruler commented on John's posting
This spur has not been used for a while because the city is not careful about keeping asphalt patches out of the flangeway. |
 |
Robert Jordan shared
I looked hard and couldn't see I posted before so I hope.... Anyway this was a fun line. Dodging traffic, in and out side streets and alleys, City traffic control people prairie wild flowers on the ROW. This scene is the cure for not remembering exactly where you took the photo.
Central Illinois Railroad 8/21/07
Rob Olewinski Cmraseye it was.....https://www.flickr.com/.../cmraseye/albums/72157624576111211
Rob Olewinski Cmraseye I have been seeing the BNSF operating as far as the scrap yard between Ashland and Damen. The tracks east of Ashland are abandoned and mostly gone.
Robert Jordan That makes sense since most of East of Ashland was to get to their little compound. Going north from that little Y was a line up to the BN that looked very interesting but was OS when I got around there. There was that weird building siding just north of Cermak, I think there was a photo in the Album, think that was east of Ashland?
Rob Olewinski Cmraseye these tracks are gone. South of the 'compound' across Cermak was Universal Carloading (building still there). It was one of the original 'Q' freight houses, my father worked there most of his working career. That line running north to the yard was what fed the freighthouse.
Rob Olewinski Cmraseye Robert Jordan there were a few industries between Halsted and Ashland, ComEd used to get coal LONG ago as well. The track did continue east across Halsted almost to the River as well at one point.
Jeff Lewis Cool shot. You were looking north on Ashland at Cermak and Blue Island. That's St. Jude's steeple in the background. [Street View] |
 |
3D Satellite
This must have been the "Universal Carloading" building. The rest of the land south of "the compound" was a slip and port facilities. |
 |
Zaky Joseph posted
On a frigid cold snowy morning in January of 2009, we see the Central Illinois Railway picking up their cars which they received in interchange from the BNSF at Western Ave, including scrap cars going to Cozzi metals and covered hoppers for Domino Sugar. An ex BRC sw 1200 #1206 (repainted into Chicago Burlington and Quincy colors) and similar to the BRC paint scheme plus another CIRY switcher prepare to depart to go switching out these industries on the former Burlington Lumber District.
Franklin Campbell The other unit must have just been transferred from the Illinois Northern side.
[I was surprised that the trains were that long as recently as 2009. I just took several photos of Cozzi Recycling when I checked out the new 25th Street Overpass. They must have moved. I wonder where they were in Chicago. I could not see any rail spur for their Bellwood, IL, facility.] |
 |
Waldolf Ursine posted
#ThrowbackThursday back to 2011 . 2 Central Illinois switches parked in there small fenced in yard at Cermak and Canalport parked in storage just after the line shut down. Note how the stacks are covered in plastic. Today the rails have been pulled up and the row is being converted to a trail. |